The importance of finite element analysis (FEA) in the field of packaging is crucial to ensure the safety, functionality, and integrity of packaging throughout its entire lifecycle, from production to distribution. Finite element analysis offers numerous advantages that contribute to optimal packaging design and effectiveness. Here are some key points on the importance of these analyses:
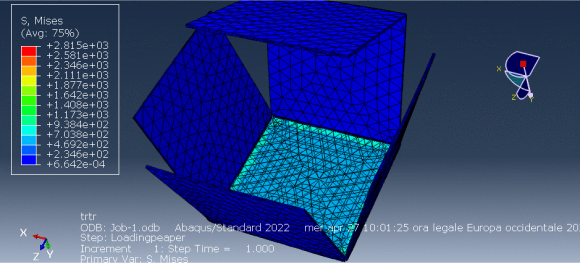
1. Design Optimization:
Finite element analysis allows engineers to optimize packaging design by reducing the material used without compromising strength and durability. This results in lighter, more cost-effective, and environmentally friendly packaging.
2. Prevention of Transport Damages:
Through simulations of drops and impacts, FEA helps predict and prevent damage to packaging during transportation, reducing product losses and improving content protection.
3. Stress and Strain Analysis:
Finite element analysis evaluates the stresses and strains on packaging under various operating conditions, ensuring they can withstand mechanical stresses without failures or unacceptable deformations.
4. Reduction of Production Costs:
By optimizing design and structural strength, FEA contributes to reducing production costs, allowing more efficient use of materials without compromising performance.
5. Compliance with Regulations and Standards:
Finite element analysis is essential to ensure that packaging meets industry regulations and standards. This is particularly important in regulated sectors such as the transportation of hazardous goods or food products.
6. Development of Innovative Packaging:
The use of FEA stimulates innovation in packaging design, enabling the creation of more creative solutions tailored to the specific needs of products and markets.
7. Time and Resource Savings:
Simulations through FEA allow the virtual testing of different configurations and scenarios, reducing the need for physical prototypes and speeding up the development process.
In summary, the use of finite element analysis in packaging represents a strategic investment to ensure the quality and effectiveness of packaging, contributing to the development of more efficient, sustainable, and industry-compliant solutions.
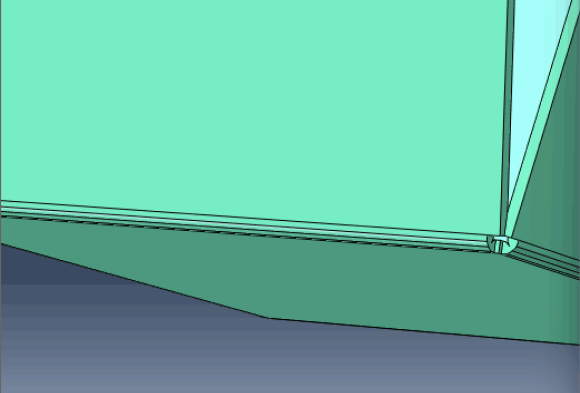
The various types of tests:
1. Stress Analysis:
Evaluation of stresses and tensions on packaging materials during handling, transportation, and storage.
2. Structural Integrity:
Verification of the structural strength of packaging, containers, and pallets to ensure they can withstand expected loads and operating conditions.
3. Durability Analysis:
Assessment of the durability of packaging under repeated cyclic loads, such as during long-distance transportation.
4. Thermal Analysis:
Study of the thermal behavior of packaging to ensure they can withstand temperature variations during transportation and storage.
5. Vibration Analysis:
Evaluation of the effects of vibrations on packages during transportation with the goal of preventing damage to the contents.
6. Drop and Impact Analysis:
Simulation of impacts and falls that may occur during the handling of packaging to ensure the protection of internal products.
7. Fluid Dynamics:
Study of liquid or gas flows within packaging to ensure suitable transport and storage conditions.
8. Optimization:
Use of finite element analysis to optimize packaging design, reducing the material used without compromising performance.
9. Material Selection:
Assessment of the performance of different materials to select those most suitable for packaging based on specific requirements.
10. Compliance and Certification:
Verification that packaging complies with industry regulations and standards, contributing to certification and regulatory compliance.